Takes Less Space While Still Increasing Yields, Reducing Labor Costs, and Saving Money on Fresh Oil
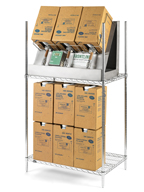
Both small and large foodservice establishments can save money on the cost of fresh cooking oil while increasing yields up to 10% with Frontline International’s Box System for Standard Packaged Oil, a hands-free, convenient, safer, and more cost-effective way to dispense fresh cooking oil for refilling fryers. Now, Frontline is rolling out a new version designed to fit a smaller footprint. The new dimensions are a space-saving 24 inches deep by 36 inches wide—but the system can still dispense up to 140 pounds (or 18+ gallons) of cooking oil.
With the patent-pending Box System for Standard Packaged Oil—winner of a 2012 Kitchen Innovations Award—operators purchase their choice of fresh oil in boxes or jugs from any vendor. Oil stored in boxes reduces overhead, needs less storage space than a tank, and reduces liability from purchasing bulk oil that can spoil. Frontline’s Box System maintains oil freshness and quality, thus providing a greater ROI and improving food quality.
Simply place boxes or jugs upside-down in Frontline racks. Several boxes can be connected to several fryers simultaneously. Then fryers are filled either automatically (direct-plumbed) or by using a convenient, no-mess dispensing wand. Upside-down storage is the key—every drop of oil gets dispensed, increasing yields up to 10%. And the hands-free, automated Box System frees kitchen staff from filling fryers all day, reducing labor and improving productivity in the kitchen. Optional digital reader technology monitors the level of fresh cooking oil available, and stores and headquarters alike can generate reports on usage, helping keep oil costs down.
About Frontline International
Frontline International, Inc. designs, manufactures, and distributes superior commercial foodservice equipment for the storage, handling, and disposal of cooking oil. With Frontline, you own your own equipment, negotiate your own oil rebates, and have the freedom to choose your own oil vendors. Frontline and its Smart Oil Management systems offer users more freedom and more control over their processes and their profits. For more information, contact Frontline International, Inc. at 187 Ascot Parkway, Cuyahoga Falls, OH 44223. Phone: +1 330-861-1100. Toll free: 1-877-776-1100. Web: www.frontlineii.com. E-mail: info@frontlineii.com.